The impact of textile production on the environment
The textile industry is currently one of many major industries under pressure to rapidly reduce its environmental impact. A European Parliamentary Research Service (EPRS) study found that the production of clothing and footwear is responsible for about 10% of annual carbon emissions – which is higher than all international flights and maritime shipping emissions combined – using around 79 billion cubic meters of water annually. In addition, clothing production is a significant contributor to industrial wastewater pollution. While these statistics are several years old and there have been some improvements, the scale of the issue hasn’t changed. This makes reducing water use, wastewater, and energy/CO₂ the most urgent priorities to address in the textile value chain.
One way clothing and footwear producers are working to address these priorities is by using more recycled raw materials, such as recycled polyester from polyethylene terephthalate (PET) bottles, within their synthetic fibers. However, the process of how these fibers are colored or dyed has not dramatically changed. In this article, we’ll explore how spin-dyeing fibers can offer a more eco-conscious alternative to coloring textiles compared to traditional bath-dyeing.
Spin-dyeing as a sustainable dyeing technology alternative
Wet or bath-dyeing is traditionally the most commonly used technology to dye fibers or yarns. It uses substantial amounts of water and energy to heat a mixture of water and chemicals to dye the yarn. However, for synthetic fibers manufactured by an extrusion process, such as polyester, polyamide, and polypropylene, there is another technology that uses no water and less energy than classic bath-dyeing: spin-dyeing. With this technology, color is added during the production of the synthetic fiber, reducing the number of steps and, as a result, the amount of energy needed to add color. The colorant is in the form of concentrate pellets added to the polymer pellets during the extrusion and melting process. The plastic mass is then shaped into filaments, spun, and texturized into an already-dyed yarn. No water is involved and no waste water is created.
Classic bath-dyeing process
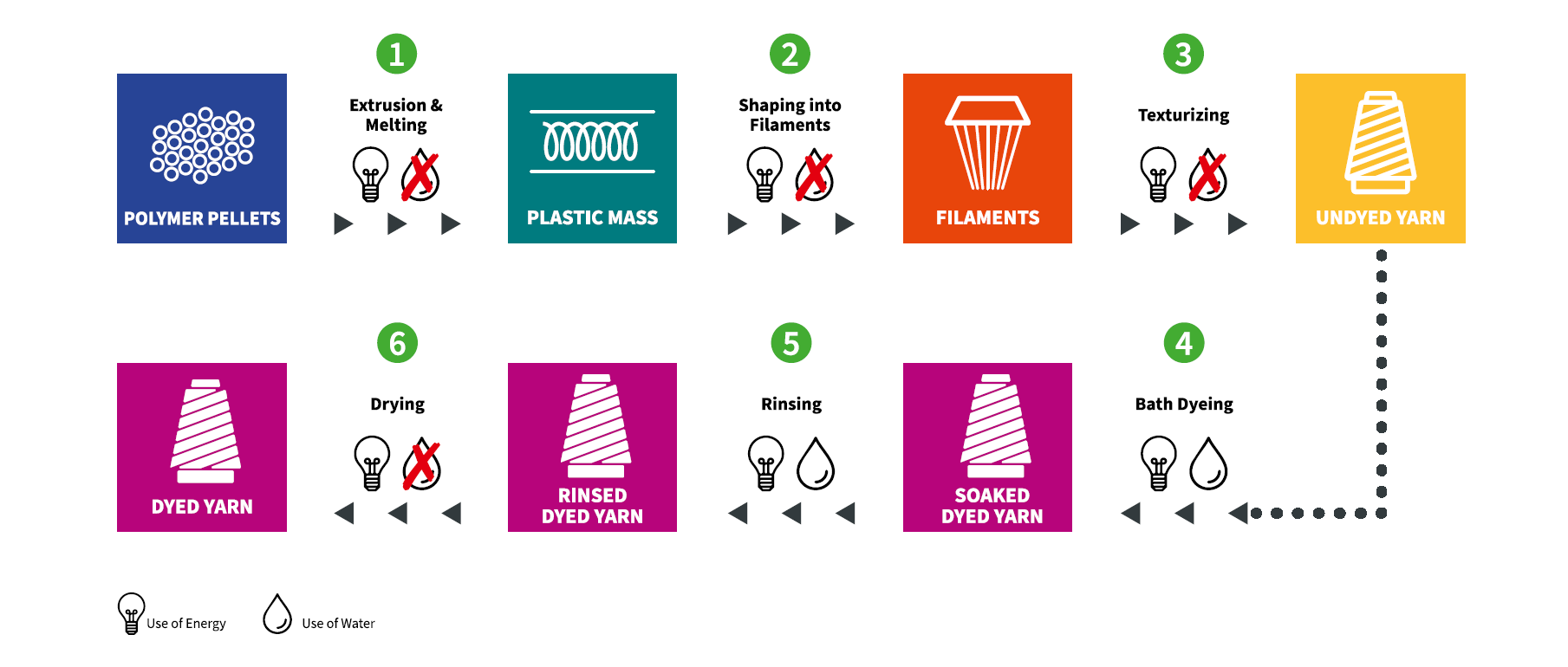
Spin-dyeing process
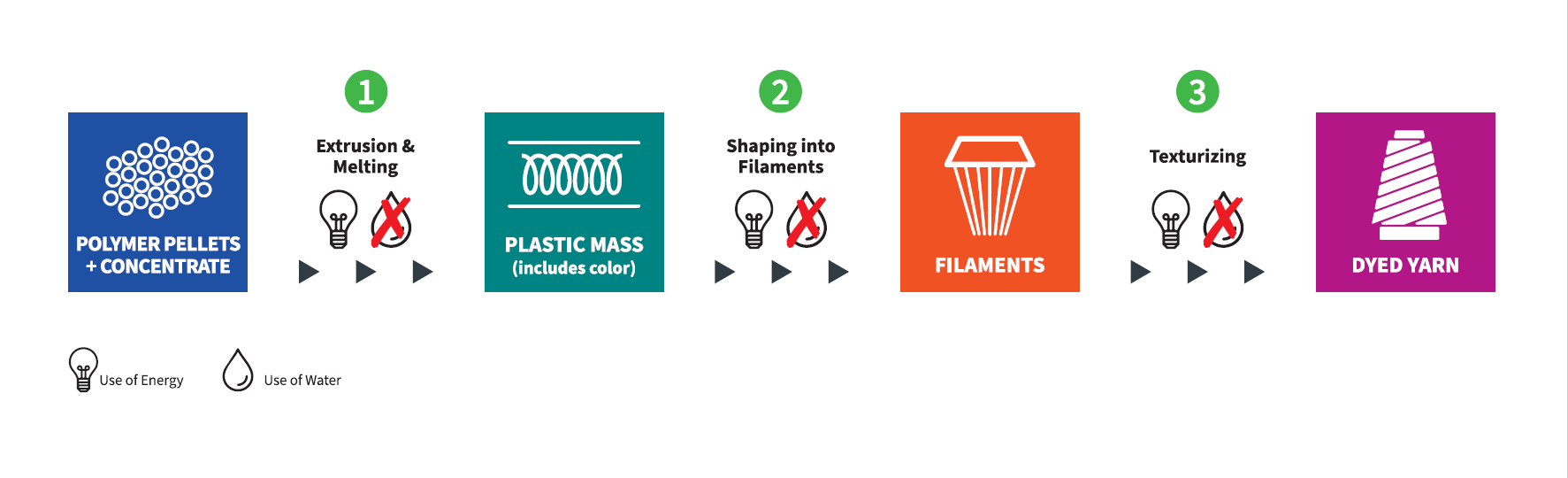
Avient’s portfolio for spin-dyeing
Avient offers color concentrates (a.k.a. masterbatches) for spin-dyeing virgin and recycled fiber-grade polymers. Our portfolio includes Renol™ Fiber Colorants specifically developed for polyester and polyamide (nylon) fibers and Remafin™ Fiber Colorants for polypropylene (PP) fibers and spunbond nonwovens. In addition, Avient’s Cesa™ Fiber Additives can enhance properties such as light stabilization, flame retardancy, or antimicrobial effectiveness to increase recycled polymers' spinning efficiency and mechanical properties. In addition, Avient has built a strong expertise in spin-dyeing based on decades of developing masterbatch solutions for the textile market and working with local and regional fiber producers and textile associations. Companies wishing to switch from bath-dyeing to spin-dyeing can rely on this expertise and our global footprint to make the switch as easy and efficient as possible.